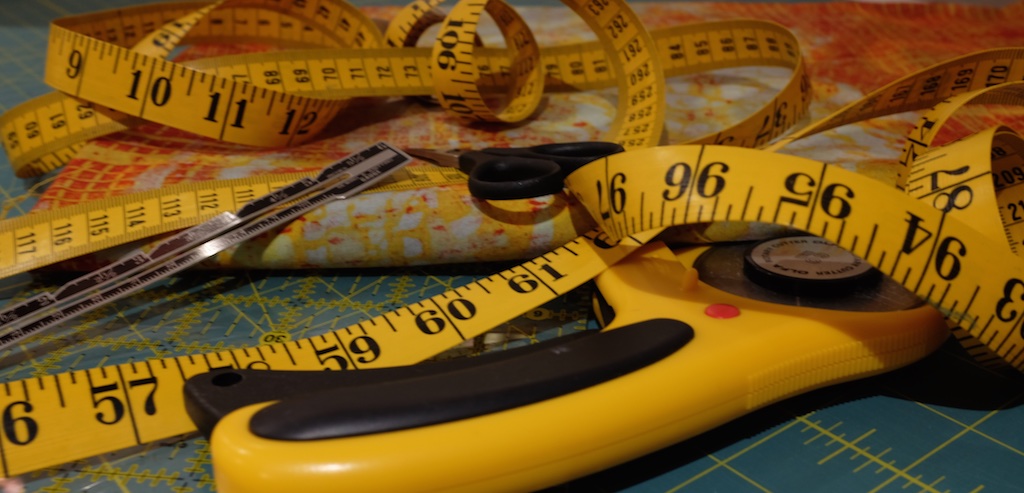
HOPEFULLY HELPFUL HOW TO
Hopefully helpful how to
How to finish an art quilt with a facing
I can’t claim that there is universal agreement about this, but I’m fairly confident in saying that the majority of folks agree that art quilts—quilts of any size that are created especially for the wall and not intended to be used as a functional quilt on a bed—look neat and professionally presented when the edges are finished with a facing rather than a typical wrapped binding. I’ve tried many finishing techniques over the years: binding, raw edge, overcast, and facing. They all take time and effort, but facing is definitely well worth the effort for the refined look that it produces on the finished product.
There are many step-by-step guides to quilt facing on the internet. I think that the folks at Bernina have created one of the better posts on the subject (https://weallsew.com/make-quilt-facing). My method is a mashup of the content on this site with bits and pieces collected from others over the years, plus some of my own ideas.
I’ve created a short video that explains the process and includes the tips and tricks that help me get good and satisfying results. When I say it’s short I mean about 35 minutes or so. If this doesn’t seem short to you, then consider that this is version 3. Version 1 was over an hour of rambling and editorializing!
In the video I show several tools that are either helpful or essential. I hope that the video and the links below are helpful to you in your own studio.
Folding layout triangle https://a.co/d/cEhpE6e
That Purple Thang https://a.co/d/bxuUBTe
Tailor’s clapper https://a.co/d/bKWxXDW
Olfa rotary cutter with pinking blade https://a.co/d/eAs1EIP
Superior hand quilting thread
https://www.superiorthreads.com/treasure-559-photographs/p/131-01-559Thread Heaven thread conditioner
Oops. The company appears to be out of business. Just look for a thread conditioner that’s not wax-based. I’ve used wax and prefer the silicone stuff.Clover Ultimate Needle Threader https://a.co/d/4zu7ZfA
KAI 7250: 10-inch Professional Shears
https://kaiscissors.com/kai-7250-10-inch-professional-shearsSewing clips https://a.co/d/cYEH70H
How to create a top sleeve for hanging art cloth
A wooden lath or a dowel fitted with metal eyes makes a great support for hanging art cloth. You just create a sleeve at the top of the cloth by turning over several inches and stitching it in place. While this is an efficient and functional solution, it presents an aesthetic challenge.
- If the eyes extend visibly beyond the edge of the cloth they create a distraction.
- If we cut the lath short enough to hide the eyes behind the cloth, inside the sleeve, then the cloth will wrinkle in the area near the eye when it is hung.
The instructions below explain how I create top sleeves in my cloth that are nicely finished, completely hide the lath and eyes, AND create no wrinkly top corners when hung. The illustrations show one side of a sample of cloth. The same treatment needs to be applied to both the left and right sides. That should be obvious, but---well, it never hurts to be completely clear when it comes to instructions.
Step 1: Prepare the hanging rod or lath.
Cut the lath to size an attach the metal eyes near the top edge of each end. The finished length of the wood plus the eyes should be about 1 inch shorter than the finished width of the cloth you are hanging. This size will place the outer edge of the each eye 1/2 inch in from the edge of the cloth--a sufficient distance to hide it from view.
Step 2: Prepare the top sleeve
With the cloth face down on the work table, fold the top edge down (i.e., wrong sides together) to form a sleeve. The size of the sleeve will be determined by the length and width of the cloth and the size of the lath you're using. A 3-inch sleeve works well for 1-2 yard lengths of medium weight cloth, 24-36 inches wide.
Press the fold along the top edge, then turn under and press a 45 degree miter.
Stitch close to the edge of the miter.
Step 3: Create notches in the sleeve
Position a ruler 0.5 inches from the pressed top edge of the sleeve and mark a 1 inch long line, measuring from the edge of the miter. This line will be used to create an opening in the sleeve that will provide access to the metal eye in the supporting lath.
Using the line you just marked as a guide, stitch a button hole along the line and extending slightly off the cloth at the mitered edge.
Clip open the button hole, cutting through the side of the miter.
Step 4: Finish the sleeve.
Finish the raw edge of the sleeve. In the photo below I've pinked the edge, but it could be surged or turned under. I prefer a pinked edge for this seam location because it reduces the chance of raveling while minimizing bulk that might be visible from the front of the cloth.
Stitch the sleeve closed along the prepared seam from the bottom of one miter to the opposite. This means that the stitching will stop about 3 inches from the edge of the cloth (or whatever sleeve depth you've chosen).
I generally stitch this seam by machine with a long stitch length. Depending on the cloth, you might choose to use an invisible seam or stitch by hand.
In the photo you can see the finished sample with the supporting lath inserted in the sleeve.
Copyright Russ Little, 2016
How to choose the right thread for your quilting project
Thread selection has always been a mystery to me. I’ll go further and say that it amounts to what can almost be called occult knowledge–known to a select few and a mist-shrouded curiosity to all others. Just where does one learn about thread weight, content, needle sizes and all of that stuff? I don’t want to engage in too much naming of names and pointing of fingers, but I will say that when I learned to sew as a kid there was Coats & Clark. That was about all you could get at the local fabric store. I didn’t know there was anything else. When I bought my first Bernina almost 20 years ago, the salesperson turned her nose up at my thread and said, with great conviction, “Ah yes, well, We recommend Guttermann.” For the full effect, you need to pronounce “we” with a roll of the tongue and air of the royal “We”. Coats & Clark and Gutermann are fine products, but I’ve discovered there are others that might cost more but are worth every last penny.
Right now I’m using up my stock of Guttermann 100% polyester for piecing. I’ve switched to Aurifil 50 wt 100% cotton for quilting. It is a virtually lint-free, sews beautifully, and produces wonderful results with Schmetz Microtex 70/10 needles. When I say lint-free I’m not kidding. In my sewing lifetime I think I’ve pulled enough lint out of sewing machines to stuff a pillow. I always thought it came from the batting and the fabric. While I know that those are contributing factors, switching to a higher quality thread has produced a tremendous reduction in messy machine lint and the problems that it can cause.
I’m also considering experimenting with some Superior Threads So Fine 50 weight. It’s a 3 filament polyester. Why would I consider switching from 100% cotton to polyester? Two words: long arm. I just purchased a long arm machine that can sew 1,500 stitches per minute. A stronger thread makes a great deal of sense at that speed.
So, what are the factors that you should consider then you choose a machine needle and thread? I offer a few things to consider below. This is by no means an exhaustive or authoritative list. I’ll update this posting as I learn more. I’m also providing a list of a few good online resources that have helped me learn more about thread.
Thread size/weight
- The lower the weight number, the thicker the thread.
- 30 weight is heavier than 50 and will be more visible on the surface of the quilt.
- 50 weight is good for quilting if you want the thread to blend into the surface.
- Choosing your thread weight for topstitching (i.e., quilting) is a design consideration.
- The choice of thread weight for garments is more about fabric weight. You wouldn’t use a light weight thread on denim unless you really want to come busting out of your jeans.
Thread composition
- Choose cotton if you plan to dye what you’re sewing.
- Choose polyester for quilting if you need strength, especially in high-speed applications.
- Choose a high-quality cotton for quilting if you prefer cotton (e.g., Superior Threads King Tut or Aurifil Maco).
Needle selection
- The larger the number, the larger the eye of the needle.
- Match the needle to the thread and the weight of the fabric.
- Refer to the thread manufacturer’s website for guidance on needle selection.
- Domestic sewing machines and long arm machines use different types of needles. Needle requirements also vary from one long arm machine to another. Always refer to your machine documentation or the manufacturer’s website to identify the correct needle for your macine.
- I’ve been using Schmetz Microtex sharp needles in my Bernina 440. It’s a nice sharp needle that cleanly pierces the cotton broadcloth that I most often use. I’ve found that Aurifil 50 wt cotton sews well with the size 70/10 Microtex.
Resources
- superiorthreads.com – In addition to creating great products, Superior Threads has perhaps the best website for general education about thread.
- owensolivia.blogspot.com/2012/10/your-sewing-thread-under-microscope.html – This woman, Nancy, has created a great resource for seeing up close what makes one brand of thread different from another.
- www.aurifil.com/SiteAurifil/HOME.html – Choosing and using Aurifil thread.
- www.taunton.com/promotions/pdf/Threads_ThreadEssentials.pdf – “Threads” magazine article about thread.
- http://www.youtube.com/watchv=dZBNUKsCyxg&list=PLDEC89F1F5C79793A&index=2&feature=plpp_video – A great video from Handi Quilter explaining how tread, needle, and tension settings combine to produce good (or bad) stitch results. The video is specifically targeted at long arm users, but the principles apply to domestic machines as well.
How to use a design wall
Two of an artist’s most valuable tools are a design wall (easel or some way of viewing your work vertically) and a camera. I worked for years without a design wall. I arranged quilt blocks on the guest bed or the floor and it seemed to work OK. As I moved away from traditional quiltmaking, I kept my old habit of just throwing things on the floor or on my studio work table. Now I know better.
The design wall
Viewed at an angle on a table, your work is subject to the optical effect of foreshortening and other distortions. You might think that you’re getting a proper look at things, but you’re really not. I’ve been known to put something on the floor and stand on a stool so I could look down at it. But, rather than risk breaking your neck falling off a stool, doesn’t it make more sense to put the work on the wall? Search the web for ideas about how to create a permanent, temporary, or movable design wall. The design wall in my studio is just foam panels attached to the wall. To that I’ve pinned a piece of white flanel. Fabric sticks to it like glue and I can pin into it if I’m layering fabric.
The camera
A camera–or a smartphone with a built-in camera–is an invaluable design tool for a several reasons:
- First, it allows you to see your work from a distance. I find the small screen of a phone better than any reducing glass for revealing those design flaws that only show up from a distance.
- Second, it allows you to capture different stages and variations in your composition as you work. Have you ever arranged elements in a design, then tried to “fix” or “improve” it, only to realize that where you started was better, but you just can’t find your way back to that starting point? Take a quick picture before you start rearranging and you’ve got a record of where you started.
- Finally, if your camera has a setting for black & white, then you’ve got a great tool for helping you assess value–the darkness and lightness in your composition. Squinting your eyes when you look at a design can also give you a sense of value. A few hours of that can also give you a terrific headache. Use the camera.
Here’s an example of a design starting to come together on my design wall.
Step 1: The fabric is placed on the wall. Some of it’s folded and tucked as necessary to start to create a composition. I don’t even need a B&W image to tell me that white space in the middle needs to go.
Step 2: This looks better, but it’s rather top-heavy. Sometimes that’s good; this isn’t one of those times.
Step 3: I’ve added another piece to the lower right to adjust the visual balance.
Step 4: Finally, my eye is drawn to the diagonal line on the right in the image above. Instead of helping my eye move through the composition, I feel stuck in that spot. A little reshaping addresses the problem.
Is it done? Probably not, but I hope you get the idea that there’s significant value in seeing your work vertically and from a distance.
And, don’t forget the grayscale image as a value check. In this case, I used my computer to convert the image from Step 4 from color to black and white. However, I could have done it on my phone in the studio for a realtime evaluation of value issues in my composition.